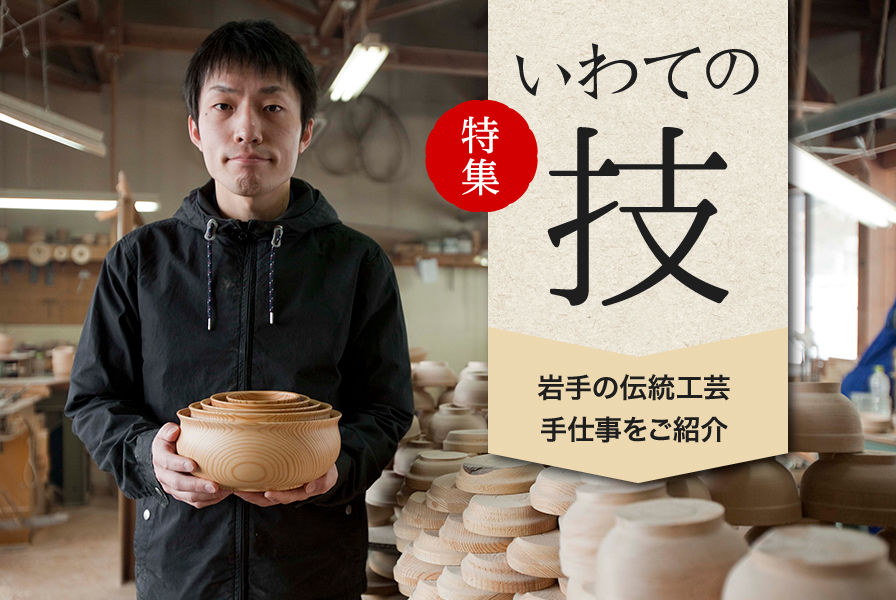
Introducing Iwate's traditional crafts and handicrafts
INDEX
Nanbu Ironware (Morioka City/Oshu City)
The history of Nambu Ironware dates back 950 years to Mizusawa, Oshu City, where it is said that it was brought to Japan when Fujiwara Kiyohira invited a foundry worker.On the other hand, Nanbu Ironware in Morioka dates back about 400 years, when Toshinao Nanbu, the lord of the Morioka domain, brought a pot from Kyoto. It is said that it began when a teacher was invited to make a tea ceremony kettle.
Iwate is rich in iron sand, iron ore, and lacquer, so ironware techniques and techniques have been passed down without interruption. In recognition of its traditional techniques, it was designated as a traditional craft in 1975.
Iwachu Co., Ltd., which manufactures and sells the traditional craft “Nanbu Ironware,” is located in Morioka City and was founded in 1902. With a history of over 110 years, we have inherited and continued to preserve the traditions and techniques of ironware making.
It is said that they release up to 1 million products into the world every year, including not only traditional products, but also products that match the lifestyle of the time, such as IH compatible products, colorful products, and modern designs. It is made. It is also exported to Europe, America, and Asia, and has gained popularity as the IWACHU brand.
①Iwachu Ironware Museum is a factory where you can see the process of making iron kettles as well as the exhibition gallery of traditional Nambu ironware designs. ②Norio Akahira of Iwachu Co., Ltd., which sells Iwate’s traditional craft, Nanbu Tekki.
③In the hall there is a large iron kettle, said to be the largest in the world. Height 1.5m, weight 350kg!
④This is an original oversized glockenspiel. You can actually play the sound♪ It seems like you can hit it freely.
In addition, the Ironware Museum is a theme park-style factory where you can see the manufacturing process of iron kettles, and is popular with tourists both domestically and internationally. Iwachu currently has six craftsmen, including two traditional craftsmen, and you can observe their skills inside the factory.
⑤⑥ When you open the next door from the hall, you will find an ironware manufacturing factory. You can actually see the craftsmen at work. It is said that there are 64 to 68 steps involved in making one iron kettle. Most of it is done by hand.
⑦This is Ryo Yaegashi, a traditional craftsman. Mr. Yaegashi calls himself “Kiyoshige”, the third generation owner.
⑧This work involves making a mold for the bottom of an iron kettle using river sand and clay from the Kitakami River. The bottom of an iron kettle is not flat, but has small rough edges, and the degree of roughness varies depending on the craftsman. Please compare them if you have a chance.
⑨The iron melted in the melting furnace is received with a ladle called a yugumi. The temperature of iron is 1400 to 1500 degrees!
⑩Pour into the mold. Only 5 to 6 pieces can be made from this one mold. It seems that it becomes unusable because it gets scratched.
⑪⑫The part where the cast iron hardens and is pulled out of the mold.
⑬⑭The hot and dangerous work can only be done by craftsmen who have acquired the skills inherited from their predecessors.
⑮ Ironware removed from the mold.
⑯After baking the lacquer and brushing with ohaguro or tea juice, carefully wipe it off with a cloth.
At the shop inside the building, you can purchase iron kettles, teapots, kitchenware, etc. You can ask about how to use and care for it, and we also recommend trying it out for yourself. There are many lineups, so why not stop by after your tour? You can also purchase products from our online shop.
⑰The factory tour was a bit nerve-wracking, but Sobachi was very happy to see the colorful iron kettles at the sales corner!
⑱The modern design and beautiful colors of iron kettles are said to be especially popular among Westerners.
⑲Rock-cast Nambu ironware teapot “Origami” designed by KEN OKUYAMA. It is used on JR East’s luxury sleeper train “Transuite Shikishima”. You can purchase it at Iwachu stores and souvenir shops at Morioka Station.
Rock Ironware Museum
Oshu City Traditional Industry Hall Nanbu Ironware Museum
In addition to displaying materials related to Oshu Mizusawa’s “Nanbu Ironware,” there is also a corner that recreates the casting process in the early Meiji period, as well as an exhibition of now valuable ironware manufactured from the Edo and Meiji periods to recent years, so you can learn more about castings. This is a facility where you can The hall has replicas of the iconic large iron kettle and cupola, which entertain visitors.
There is also a handshake statue of Shohei Otani, a professional baseball player from Oshu City, made using Nanbu Tekki technology, so be sure to shake his hand.
①The central object is a reproduction of a cupola (a Tatara-style koshiki (foot-operated bellows) used until the early Taisho period).
②A large iron kettle is displayed next to it.
③ Inside the museum, you can see each process of making ironware.
④ Sobachi is also very interested.
There is also an exhibition of period ironware.
⑥ Sobacchi also shook hands with the statue of Shohei Otani!
⑦There is a shop attached where you can purchase.
Iwayado Tansu (Morioka City/Oshu City)
Iwatado Tansu is a traditional craft representing Iwate. This time, we spoke to Mr. Ayaichiro Mishina, the 13th generation of Iwayado Wardrobe Seisakusho Co., Ltd.
Iwayado Tansu Seisakusho is said to have started around 1783 in the middle of the Edo period. Although some designs and sizes have been modified to suit the times, the technology has remained unchanged and has been passed down from generation to generation.
①②The many thin and long boards that are leaning here are all drawings of chests of drawers. The work begins with the materials used for chests of drawers and chests of drawers, called kidori, according to the dimensions written on the front and back of each board.
③In the spacious workshop, each work is done in separate rooms, and all processes are consistent and handmade.
④Although most of the craftsmen are qualified as traditional craftsmen and have over 10 years of experience, there are also young craftsmen who joined the company three years ago.
⑤⑥This is how Iwayado chest of drawers production began around 1783, and the techniques have been passed down from generation to generation.
⑦In front of the workshop is wood that will be used as materials. It takes years to dry.
The materials used include zelkova, paulownia, plug, magnolia, and cedar. Most of the wood is sourced from Iwate Prefecture, and it takes many years to dry before being made into furniture. In addition, Nambu ironware metal fittings are used for the decorative metal fittings that are a major feature of Iwayado chest of drawers. There is also a technique called handmade metal fittings, in which decorative metal fittings are hammered out of iron or copper plates. The metal fittings are designed with dragon or lion eyes, family crests, etc. to wish the user prosperity.
In addition to the furniture in the showroom, many people also order furniture according to their purpose and location.
⑧Next, I visited the showroom.
⑨The beauty of the wood grain, the texture and luster of the lacquer, and the solidity of the metal fittings are the charms of Iwayado chest of drawers.
⑩ Karakuri chest of drawers, which is said to be very popular. There’s a storage space in this place!
⑪Karakuri chest of drawers are sometimes passed down from generation to generation, and sometimes new ones are created based on the ideas of craftsmen.
We also make interior goods such as clocks and trivets so that you can use Iwayado Tansu more easily. While preserving tradition, Mr. Mishina is also starting new things such as making original accessories in order to let young people know about the appeal of Iwayado Tansu.
⑫Using Iwayado Tansu’s techniques, everyday tools such as pot holders and paper weights are also made. It can also be used as an accent for your interior.
⑬These are small items such as brooches made from Iwayado Tansu Seisakusho’s original scrap materials. It is popular because it is lightweight, easy to use, and has a unique design.
Iwayado Drawer Seisakusho Co., Ltd.
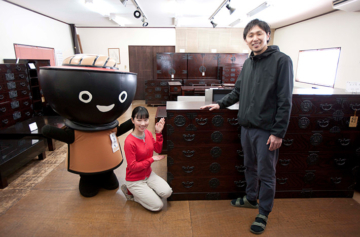
- Address
- 63-1 Ebishima, Atago, Esashi-ku, Oshu / 204-1 Yanagawa, Atago, Esashi-ku, Oshu (ITS: Showroom)
- Inquiries
- 0197-35-6016 / 0197-35-7357 (ITS: Showroom)
- Access
- Approximately 10 minutes by car from Mizusawa IC
Hidehira lacquerware (Ichinoseki City, Hiraizumi Town, etc.)
The name Hidehira lacquerware is derived from the Hidehira bowl, which has been passed down in the Hiraizumi region since ancient times, and is characterized by the gorgeous Hidehira pattern, which uses a cloud shape called Genji cloud and rhombus-shaped gold leaf, and lacquer-painted flower patterns. It is said that this is because Fujiwara Hidehira, who was at the height of his prosperity at the end of the Heian period, commissioned craftsmen invited from Kyoto to build the Konjikido Hall. One of the reasons for its development was that the Hiraizumi region at the time had abundant materials such as lacquer and gold. This technique has been passed down to this day, and in addition to bowls, a variety of other products are made using this technique.
A soup bowl with a traditional pattern of Hidehira lacquerware, a diamond pattern and a Genji cloud.
Joboji lacquerware (Ninohe City, Hachimantai City, etc.)
It is said that when Tendaiji Temple was built in Joboji Town in 728 (Nara period), the lacquerware making techniques were passed down to the monks who were sent there to make their own vessels. The vessels called “Oyamagoki” made by monks are a set of three bowls: a rice bowl, a soup bowl, and a plate, and are nested so that they can be stacked on top of each other. As the vessels were sold on the grounds of Tendaiji Temple and on the approach to the shrine, they spread to the surrounding residents and became ingrained in their daily lives. Joboji lacquerware is durable and has a beautiful color, and the luster is a little muted at first, but as you use it, it develops a rich luster. Lacquerware is characterized by not having many decorations, and the main colors are black and vermilion.It is fluffy and feels soft in the hand, making it perfect for everyday use.
At Tekiseisha, which displays and sells Joboji lacquerware, you can try your hand at painting on Joboji lacquerware. The finished product will be sent to you at a later date, so why not use it as a memento of your trip?
①You can try your hand at painting while being taught.
② The coaster is completed. There are many different personalities!
③ A clean lacquer bowl that can be used for any purpose, whether it be for rice or soup.
④The shop is full of beautiful lacquerware!
Special Feature on Iwate Techniques – 2 Iwate Craftsmen ② Central Prefecture/Southern Prefecture